GloTech RE-DO™ Process
One custom solution GloTech provides is to RE-DO™ an existing project that isn’t meeting our customer’s needs. Whether the existing product wasn’t designed well to begin with, or an off-the-shelf product was used to cut development time and costs, many companies can benefit from a well-designed solution created specifically for their application and concerns.
Because of this, GloTech developed the RE-DO™ process to scan and recreate an existing product, then apply modern design considerations and our experience to improve the design, creating market-leading new products tailored to solve our customer’s pain points.
Do you want support on RE-DO™ product in your business?
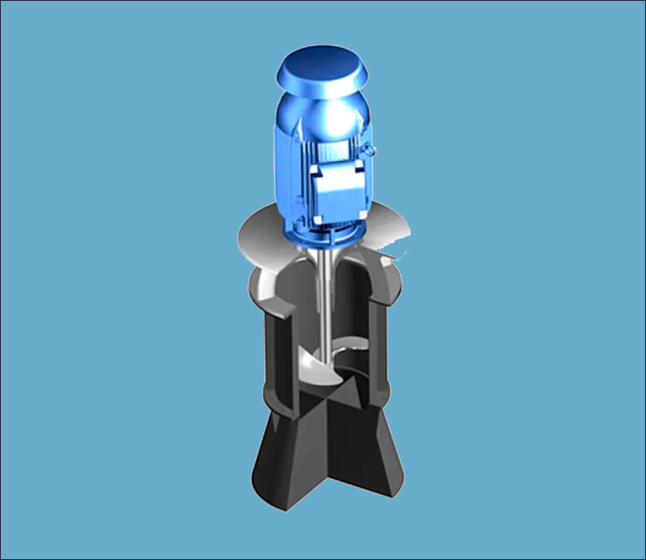
Case Study
Aerator Propeller Optimization Project
Problem
We were first engaged to “analyze” their existing 50HP aerator prop, and to potentially provide an improved design solutions.
Main challenges reported by customer on their existing product were:
- Excessive vibration during operation, causing pre-mature motor and bearing failure
- Needed Time Consuming manual re-pitch operation on every blade
GloTech Solution
GloTech was able to reverse engineer the existing prop by scanning a sample using our FARO Arm scanner. We then use CAd to model and visualize the design for analysis. Our team identified a major blade-to-blade height discrepancy, which was most likely causing unbalanced hydraulic loads (therefore vibration) during operation.
We also identified the blade profile could be optimized to improve performance and improved manufacturing processes could potentially eliminate the need to re-pitch each blade. Our customer then approved our concepts and commissioned the new design.
Next GloTech performed a variety of design optimizations to pre-pitched and balanced the prop to perfectly solve the performance issues. By refining the blade profile through multiple iterations of CFD simulations and physical testing, we were able to achieve optimal propeller performance in for both vibration and power consumption. Then in a manufacturing process, we used lost-wax investment castings to ensure dimensional accuracy and blade surface finish.
Further employing a set of high-precision, CNC machined “pitching blocks” during the production process, we were able to ensure accurate pitch and rake without the need for subsequent manual corrections. The dynamic balancing process and CMM inspections further ensure perfect blade-to-blade consistency and dimensional accuracy.
Results
We surpassed customer’s expectations for product performance and consistency. Customer was happy with not only the part cost savings, but also the peace of mind when it comes of product acceptance, quality, and field performance and has the new design in operation. The Customer also began additional projects for GloTech to improve their other propeller products.
See the Full Project Report:

Full Modeling of the Aerator Assembly after design improvements showcases the final design in context
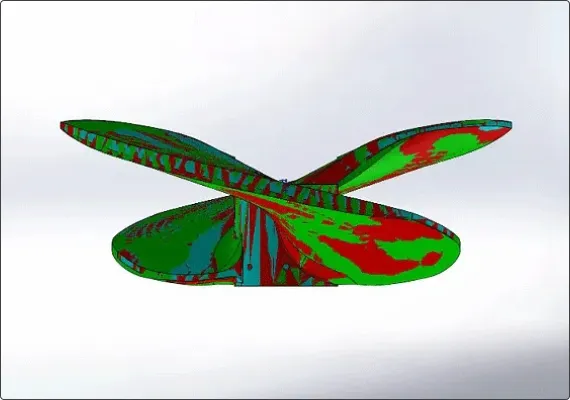
By Scanning individual points from the existing original design, an accurate baseline model can be rapidly developed to make improvements to.