Computational Simulations
Harnessing the Power of Iterative Computational Modeling!
At GloTech, we leverage advanced simulation capabilities like Finite Element Analysis (FEA) and Computational Fluid Dynamics (CFD) daily to meet and exceed our customers’ needs. FEA allows us to analyze and predict the behavior of complex structures under various conditions, ensuring that our products are robust, reliable, and optimized for performance. By simulating real-world forces, such as pressure, temperature, and vibration, we can identify potential points of failure and make necessary adjustments before physical prototypes are built. This not only accelerates the development process but also significantly reduces costs and enhances the overall quality and durability of our products.
CFD, on the other hand, enables us to understand and optimize fluid flow within our systems. Whether it’s water treatment solutions or intricate valve mechanisms, CFD simulations allow us to visualize fluid dynamics, identify inefficiencies, and make informed design improvements. By accurately predicting how fluids interact with our products, we ensure optimal performance, energy efficiency, and compliance with stringent industry standards. Together, FEA and CFD combine to be key solutions helping us deliver cutting-edge results that address the evolving needs of our customers with precision and reliability. Contact us today to learn more about how our simulation capabilities can enhance your projects, or request a quote to get started on a tailored solution for your needs.
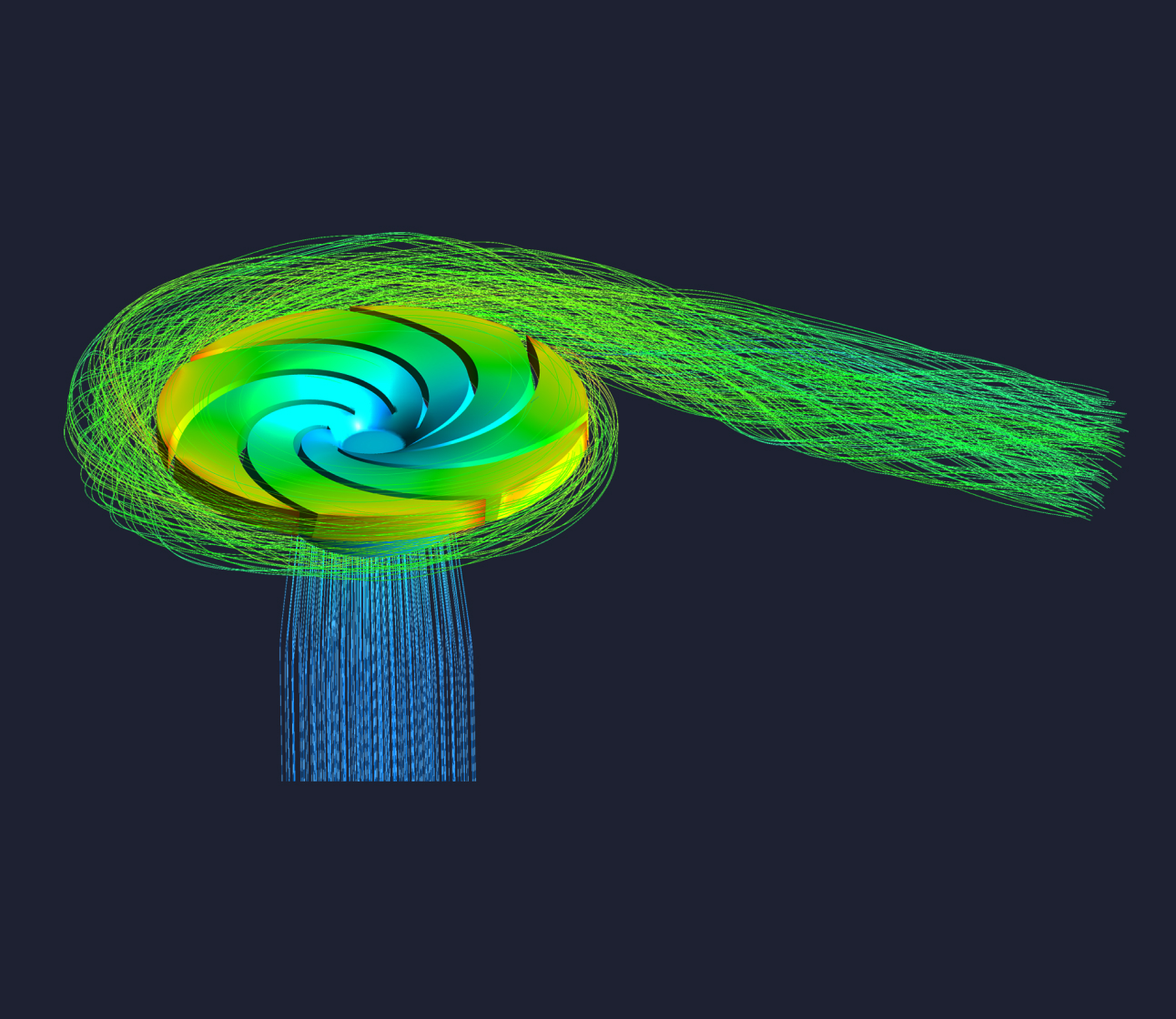
Case Study
Max Prime Project
Problem
GloTech offers End Suction Centrifugal Pumps, typically one-stage with a single impeller, heavily used for dewatering in the construction and mining industries. These pumps are often part of a system that includes the pump, check valve, belt drive (usually powered by a diesel engine), and a priming system. While excellent at pumping water, End Suction Centrifugal Pumps cannot pump air, necessitating a priming system to draw liquid into the pump.
During the design cycle for our C2300 series pumps, we encountered a significant challenge. Our pump, like most diaphragm pumps, uses a reinforced rubber layer that moves up and down to create suction by moving gas in and out. However, during testing, this rubber layer was wearing out too quickly under normal operation.
GloTech Solution
To address this issue, GloTech leveraged our advanced computer modeling and Finite Element Analysis to Accurately model the stress concentrations, use rapidly design iterations, and optimize the design. By designing with accurate 3D models, we were able to quickly load our designs into our dynamic stress analysis tools to identify stress concentrations during operations. This detailed insight was critical in understanding the wear patterns in the rubber layer, and being able to select the physical design variables affecting those stresses. By testing 16 different designs in a short period of time, we were able to significantly sped up the design timeline without the cost or wait for prototyping. This approach enabled us to explore the full range of possible variables efficiently. Then through FEA, we optimized the stress distribution in the pump fine tuning the critical design criterial to reduce the overall stresses in the rubber and reduce the localized stress concentrations by a factor of five directly addressing the premature wear issue.
Results
Our next (and final) prototype, built to the new design specifications, successfully passed extended life testing without showing signs of wear and tear previously observed. This new design met all design targets and is now a standard part, achieving significant success in the market.
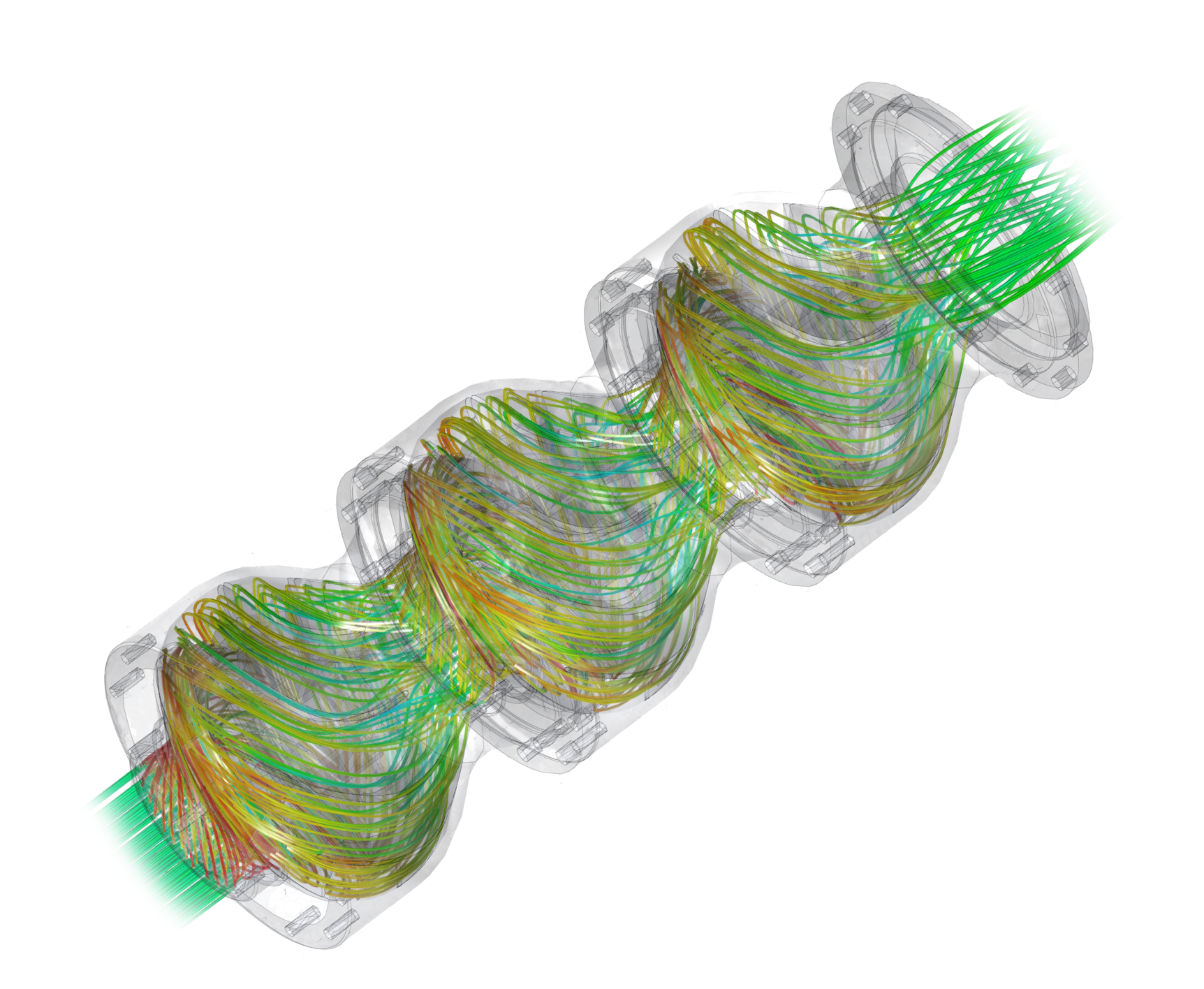